An Air Force veteran is the first to receive a definitive 3D-printed transtibial prosthetic socket fabricated using the integrated workflow at the US Department of Veterans Affairs (VA) facility at the VA Puget Sound Health Care System. X_Labs, the innovations arm at the VA Puget Sound, pioneered the workflow using digital tools customized for veterans. Along with spearheading the development, X_Labs also coordinated the collaboration across the VA and private sector.
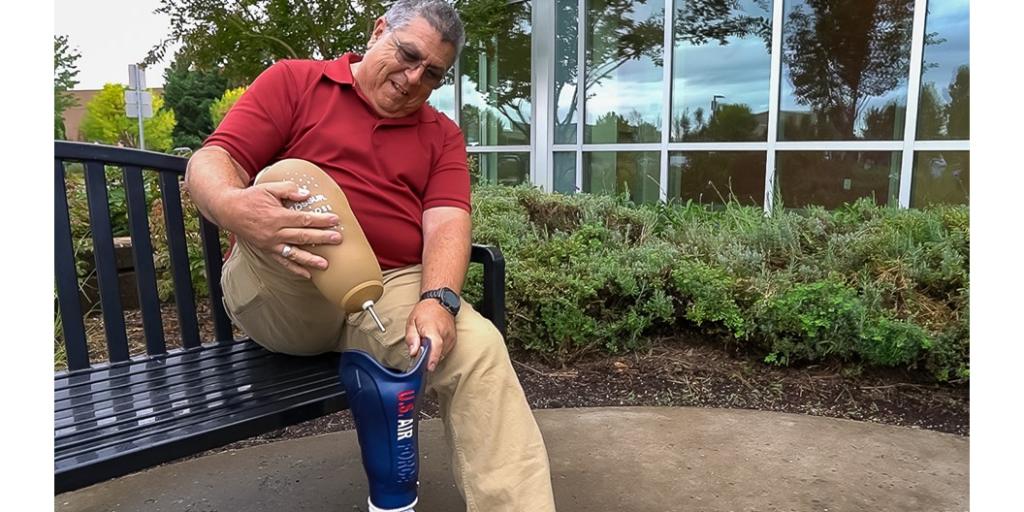
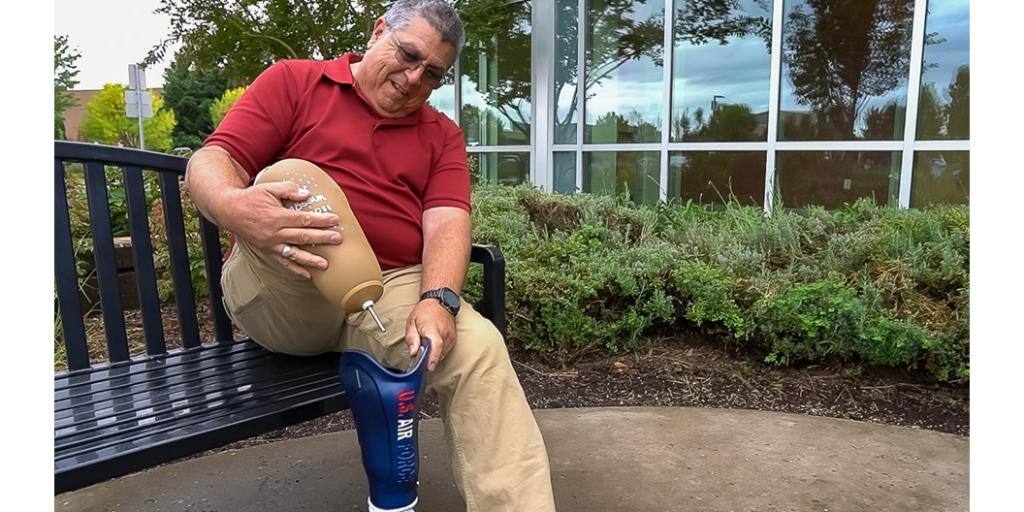
Stuart is the first veteran to receive a 3D-printed prosthetic socket fabricated using the VA’s integrated workflow. Photograph by VA Puget Sound photographer Oscar Valenzuela.
“The process began with the X_Labs team designing a streamlined, integrated process that allowed experts across multiple VA facilities and industry partners to contribute seamlessly,” said Alex Berardo-Cates, product development engineer, XLabs, who headed up the transtibial socket workflow for the prototype. “We sourced industry experts—HP, Red Duke Strategies, and Radii Devices—to complement and expedite our VA capabilities through an integrated workflow.”
George Gregory, CPO, Roseburg VA Health Care System, first gathered key data about retired Air Force Staff Sgt. William Stuart’s residual limb shape, his needs and activities, wearability requirements, and any sensitive areas of the limb using a diagnostic check socket. The data was then sent to the VA’s Northwest Integrated Network (VISN 20) Central Fabrication Unit (CFU) where it was cast with plaster. The mold was then 3D scanned to generate a digital model of the final shape in preparation for 3D printing. Matt Kovari, CTPO, used the digital model to 3D print the socket out of a high-performance plastic.
Stuart’s socket was further personalized for fit, with the US Air Force emblem imprinted on the front and wings on the back.
From there, industry partner HP finished the part and enhanced the socket’s durability and aesthetics, applying a specialized dye and vapor smoothing process before returning the final socket to VISN 20 CFU for assembly. Once assembled, the device was sent back to Gregory at the VA Eugene Community Clinic where Stuart tried it on the for the first time. With his feedback guiding refinements, the team perfected the socket by the third iteration.
Maintaining the benefits of the VA digital infrastructure, the VA Puget Sound X_Labs team built the toolsets and workflow from the ground up, ensuring robust data and network security. Everything was tested and documented so it can be replicated across the VA to support personalized healthcare solutions for veterans and their providers to access the tools and resources.
VA Puget Sound X_Labs hopes to finalize the protype before the end of the year, laying the groundwork for its availability across the VA in 2026.
“Once we feel we’ve mastered this socket, we would like to move to another device. It is a big investment on the front end, with long-term, lasting returns,” added Berardo-Cates.